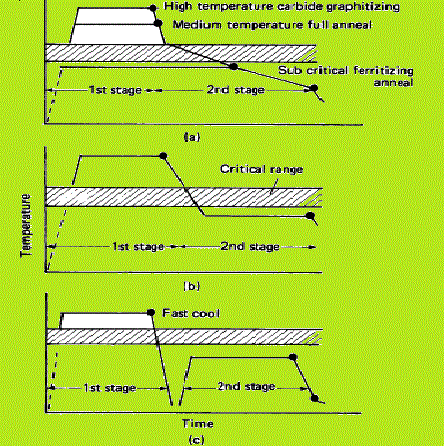
Heat Treatment Basics for Metallic Material
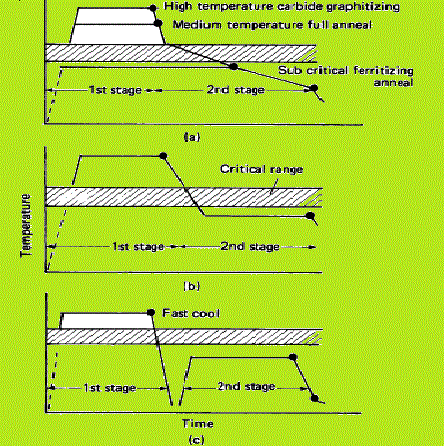
Scope:
In this article, the basic principles of heat treatment will be briefly discussed, which are mainly related to the "base material" of recorded welded construction (metal material) for industrial application.
In Part-0, we discussed the basics from a theory point of view originally taught in engineering colleges.
In the present article i.e. Part - 1, we will discuss heat treatment from an industrial application point of view, mainly for materials connecting to welding (base material).
Importance of Heat Treatment:
To relieve residual stresses (ferritic steels).
Dissolving carbides (chromium carbides) to avoid sensitization (intercellular corrosion), especially in austenitic steel.
Especially for the low and high alloy steel (like Cr-Mo, 13Cr-4Ni, etc.) is suitable for service (tempered martensite) to make steel microstructure.
Heat Treatment based on when it is performed:
Intermediate Heat Treatment: For high restraint joints during cold or in Cr-Mo steel (nozzle to shell/dish joint).
Post Weld Heat Treatment: Performed immediately or after allowing the temperature to weld at room temperature with the purpose described in the above points.
Classification of Heat Treatment Process (Base Material):
👉Annealing
👉Hardening and
👉Quenching/Tempering.
Where;
A1= The temperature at which austenite beings to form during heating,
A3= The temperature at which the transformation of ferrite to austenite is complete during heating.
Annealing:
It is a general term denoting thermal treatments that consist of heating at a specifics rate, holding at the specific temperature for a finite period of time, and cooling at a specified rate primarily to the softened metallic materials.
The above figure shows an example of Annealing (Homogenizing)
Here:A1 = the temperature at which austenite beings to form during heating.
👉Achieving uniform microstructure:
Diffusion annealing
Normal annealing
👉To enhance workability
Coarse grain annealing
Soft annealing
Recrystallization annealing
Crystal recovery annealing
👉Minimizing the stresses
Stress relief annealing
Stress-relieving treatment
👉Microstructural changes
Tempering
👉Special Cases
Controlled Cooling
Quenching
Perlite annealing
Bainitic microstructure transformation.
Normalizing: Heating to 30 to 50°K above A3 (astonishing) temperature in case of hypo eutectoid (carbon steel) steel. The soaking time at the time of holding temperature will be such that the whole job is heated uniformly to the normalizing temperature. And after that, it will be cooled in the resting air.
The aim of normalizing is thus also to achieve an even microstructure with the fine lamellar pearlite.
👉Above figure represents a normalizing cycle.
👉Normalizing is recommended in the following cases:
In the case of coarse grain.
In the case of solidification microstructure, eg weld joint or cast steel
In the case of steels embrittled due to aging and
In the case of all constructional steels with an insufficient toughness or too low a yield point.
Stress Relief annealing: It is a process of heating and holding at annealing below from A1 with subsequent slow cooling so that the internal stresses are reduced without significant changes to the other properties.
![]() |
Stress relief annealing cycle |
👉Internal stresses can be generated due to uneven heating and cooling of the material e.g. during the welding, like soldering, solidification, or quenching, but also due to the cold forming. This stress often causes distortion or lead to the formation of cracks in the components.
Coarse grain annealing: it is carried out in the temperature range of 950° and 1100° C (above A3) with the hold time of about 1hr to 4 hr. (Prolonged period of the time) and the cooling slowly to achieve coarse grain structures.
Also, visit for more inquiry
Heat treatments Basics for the metallic material-0
Welding Base metal Thickness limit
The aim of the coarse grain formation is to produce a coarse grain with low hardness and toughness properties. These type of microstructures is advantageous for the milling, since the chips produced are small, thus leading to lower cuttings forces.
Soft annealing (annealing on globular cementite): It is a process that means to reduces the hardness of the material to a defined value in which annealing is performed at temperature closely below or just above. A1or held around the A1, with the subsequent slow cooling.
👉The aim of soft annealing is to obtain a soft microstructure suitable for further processing, such as milling or cold deformation.
👉The optimum condition of the microstructure consists of homogeneously distributed, fine-grained, globular carbides embedded in a ferritic matrix and such a microstructure can be split, bent, compressed, flanged, extruded, or twisted with ease.
👉Above figure represents the soft annealing cycle of low carbon steel.
👉The above figure represents heat treatment (2nd picture) which is mainly used in steels with carbon content above 0.5%, for example, with roller bearing steels.
Diffusion annealing: Annealing in the temperature range of 1050°C to 1250°C, with a prolonged hold time of around 50hr, in order to balance local differences in the chemical composition due to segregation by diffusion.
👉Due to high temperatures during diffusion annealing a formation of coarse grains is unavoidable. Coarse grain can be removed by normalizing.
👉The below figure-8 represents a diffusion annealing cycle.
Recrystallization annealing: It is a process of heat treatment to realize new grain formation in a cold-formed workpiece through the nucleation and growth without any phase change.
👉During cold forming as the hardness increases which reduces the formability and for this reason, cold deformation cannot be carried out indefinitely, and hence after certain deformation recrystallization annealing in order to restore the original material properties.
👉Min recrystallization temperature = 0.4 times absolute melting temperature.
👉Three Stages involved are as mentioned below:
Crystal Recovery: It involves rectifying dimensional lattice structure imperfections and rearranging dislocations.
Primary recrystallization stages: This leads to complete grain reforming.
Secondary recrystallization stages: In these stages, above the recrystallization temperature, the small grains formed by the primary recrystallization combine to form a small number of large grains.
Solution annealing: The main aim of solution annealing is to bring and hold the separated microstructures in the solution (like a homogenizing).
👉This is particularly desirable with austenitic Cr-Ni steels (above 1000 C) because it enables the required corrosion resistance to be achieved.
👉The purpose is to obtain a standardized austenite crystal deprived of precipitations by rapidly cooling in chilled/room temperature water.
👉The above figure-10 represents a solution annealing cycle.
(Note: The purpose of this article heat treatment for metallic material, is to give a general guideline to the readers, and it shall not be considered as a substitute for the code. For full terms and conditions please read the relevant code and its clauses).
Post a Comment
Please do not enter any spam link in the comment box.